Radiology Quality Assurance Program: What Should the RT Know?
All healthcare facilities have a radiology quality assurance program to provide confidence in radiation safety. Quality assurance essentially consists of an organized set of activities and processes that ensure X-ray equipment is functioning properly and providing satisfactory diagnostic information in a timely manner with minimum radiation dose to patients.
In addition to the testing and monitoring of X-ray equipment, quality control includes administrative procedures to ensure evaluation is performed properly and corrective steps are taken. Without a radiology quality assurance program, artifacts may be added to images or critical features may be missing. Poor image quality can result in delayed diagnosis, improper treatment, repeat imaging, and unnecessary radiation exposure. Ultimately, the goal of the radiology quality assurance program is to ensure that the information provided by X-ray equipment is of high quality, accurate, and timely. It is worth remembering that digital radiography requires some specific testing.
Initial planning, implementation, and ongoing operation of a radiology quality assurance program is associated with costs, both in terms of time and money. However, at many facilities, an efficient QA program actually brings about an overall reduction in operating costs. The expenses on personnel, test equipment, and test images are offset by savings on repeat imaging and use of supplies, lower workload, increased lifespan of equipment, and greater workflow efficiency and patient throughput.
Importance of Quality Control
The radiology quality assurance program at a healthcare facility is designed to ensure optimal performance by all equipment and every radiographer. This is of immense value in reducing radiation dose, improving the information obtained from images, and lowering operational costs. Poor equipment performance is a significant cause of poor image quality. Poor quality images do not provide all the possible diagnostic information to providers. In addition, poor image quality may lead to repeat imaging and therefore increased radiation exposure and cost. Finally, when radiographs of inadequate quality are produced due to poor equipment performance or suboptimal technique, the patient may be exposed to unnecessary radiation. Therefore, a good quality control program is extremely important for the delivery of quality healthcare.
What Should the Radiologic Technologist Know About Quality Assurance?
Radiologic technologists should familiarize themselves with the following aspects of the radiology quality assurance program at their facility:
- Responsibilities and authority of various staff in the department. Every staff member should understand their duties. The responsibilities of general operations and quality assurance should be clearly defined and communicated to all workers.
- Policies for minimizing occupational exposure, i.e., pregnant workers, training, technique and use of equipment, dosimetry, use of protective garments, policies for holding patients and remaining in the room during exposure.
- Strategies for minimizing patient exposure, i.e., justification and optimization, policies for pregnant patients, use of protective equipment, technique, patient positioning, technique charts, and reject analysis.
- Checklists for equipment testing, including guidelines on which equipment is to be tested, how often testing is performed, performance standards, parameters to be measured, corrective actions, optimum performance, and calibration of test equipment.
- Policies for record keeping and retention of records, including review of QA program and QC procedures.
- Acceptability limits, i.e., upper and lower limits of acceptable data, and corrective actions to be taken if limits are exceeded. For example, after repeating a test for confirmation, if performance failure persists, corrective action will depend on whether the failure is marginal or substantial, based on acceptability limits. These are outlined in the radiology quality assurance program.
Quality Control for Equipment
Quality control tests and procedures for X-ray equipment are designed to verify the mechanical stability of the device and the integrity of the safety mechanisms, such as interlocks and audio alarms. In addition, QC tests verify the performance of display monitors and other ancillary equipment. Importantly, of course, the diagnostic performance of the system is tested, including a measurement of radiation dose. This is all a part of the radiology quality assurance program.
Daily QC Tests
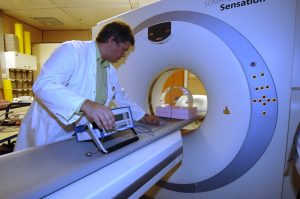
Daily quality control tests for digital radiography equipment include equipment warm up of all components routinely used during imaging, including display monitors and printers. Warm up must be performed every time the equipment has been idle for a period of time. The warm up test is performed according to the procedure recommended by the manufacturer and may require a phantom. Acrylic and aluminum phantoms have been developed based on the FDA’s NEXT surveys (nationwide evaluation of X-ray trends). These phantoms mimic passage of X-rays through human tissue. Phantoms which contain objects of known size and contrast are used to evaluate image quality.
In addition to warm up testing, as part of the radiology quality assurance program, all meters and audio and visual indicators on digital X-ray equipment are tested daily. Visual inspection of the X-ray equipment is carried out every day to identify any loose components or vibration during operation. Daily assessment of digital equipment also includes an overall visual inspection of electronic display devices used to interpret images. Test patterns, such as TG18-QC or SMPTE, are displayed to assess image quality and identify any artifacts.
Weekly QC Tests
Weekly quality control tests for digital radiography equipment include a visual inspection of the imaging system to ensure there is no dirt or dust on the image receptor that could result in poor image quality. The view box is also visually inspected every week for proper illumination and cleanliness. The operation of the laser film printer is evaluated with a test pattern image to ensure there are no artifacts or geometric distortion and that the 5% and 95% grayscale patches are visible inside the 0% and 100% patches, respectively.
Monthly QC Tests
Monthly quality control tests for digital radiography equipment include repeat analysis, including the reason and corrective actions instituted for repeat examinations. This is an important component of the radiology quality assurance program. Monthly retake analysis helps identify trends and avoid repetition of errors. A retake rate of 5 percent or less is advisable. In addition, the performance of electronic display devices is tested monthly with test patterns. The laser film printer is tested for image quality with test patterns.
Quarterly QC Tests
Quarterly quality control tests for digital radiography equipment include testing collimator operation to ensure smooth movement of the collimator blade. The SID is tested at various distances to assure that there is correct tracking and automatic maintenance of field size by the collimator with change in SID. The interlocks to doors are tested every quarter to ensure X-ray production by the equipment ceases when a door is open.
Annual QC Tests
Annual tests that are part of the radiology quality control program for digital radiography equipment include:
- Accuracy of loading factors, i.e., deviation in voltage, current, and loading time is within limits for different combinations of loading factors.
- Radiation output is high enough to minimize motion artifact.
- Beam filtration (measuring the half-value layer of aluminum).
- Automatic exposure control is assessed according to the manufacturer’s instructions.
- Alignment of the light field and X-ray field to ensure misalignment does not exceed the specified limit.
- Beam collimation to evaluate alignment of the beam-limiting device to the center of the X-ray field and accuracy of the positive beam limiting system, if present.
- Anti-scatter grid for uniformity and smooth movement.
- Detector response over a range of values of tube loading.
- Accuracy of exposure index with respect to dose to image receptor is within established range.
- Dynamic range, i.e., the maximum difference in attenuation that can be imaged simultaneously by the system.
More Annual QC Tests
- Noise and artifacts by measuring signal-to-noise ratio and ensuring noise is within established limits and signal is uniform in different parts of the area of interest.
- Spatial resolution (differentiating an object from the adjacent tissue when there is a large difference in attenuation relative to noise).
- Contrast (differentiating an object from the adjacent tissue when there is a small difference in attenuation relative to noise).
- Ensure lack of residual image on the digital detector from previous exposure.
- Entrance skin air kerma is within established limits (tested with phantom dose measurement for frequently performed procedures). These values are used to develop diagnostic reference levels at the facility.
- View boxes for luminescence, uniformity and homogeneity of light output, and ambient light in the reading room.
- Performance of electronic display devices with test patterns.
- Personal protective equipment for defects with visual inspection and radiography.
- Structural integrity, movement of components, cleanliness, and other general preventive measures for digital X-ray equipment and ancillary devices.
Quality Control for Digital Radiography Systems
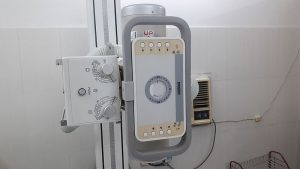
It is noteworthy that there is some extra quality control required in digital radiography systems (compared to film-screen equipment), including dose calibration according to the manufacturer’s guidelines using a customized image quality phantom. Spatial resolution, contrast, uniformity, and artifacts are other tests that are part of the radiology quality assurance program and unique to DR systems.
A reactive approach to quality control is not desirable because with this approach the patient essentially replaces the phantom as a test tool. A good quality control program is proactive. Quality control tests are performed according to a schedule under standardized conditions with objective pass/fail criteria. In other words, the quality control program in a digital radiography department ensures that performance is tested before the equipment is used to image patients.
We offer a range of online courses for X-ray technologists to earn ARRT® category A credits and update their knowledge on various subjects. Please visit our X-ray Continuing Education page to get started right away.
Here is more about radiologic technologist ce credits.